Today, computers have become an important tool for modern office, which has also led to the development of a large number of emerging industries. Commercial web printing for commercial paper is a new type of printing product with web as raw material, strict process requirements, and high product quality requirements. It is widely used in areas where computer applications such as banking, transportation, post and telecommunications, and aviation are popular. The bill printing companies that serve the sector have also rapidly emerged. However, many domestic manufacturers have neglected the production management, leading to unstable product quality, and ultimately affecting the user's use of efficiency, and even caused the product to be scrapped. Therefore, it is necessary to correctly grasp the technical characteristics and quality requirements of commercial paper printing. This paper only discusses the problem of matching pages in the production of computer commercial paper for commercial use.
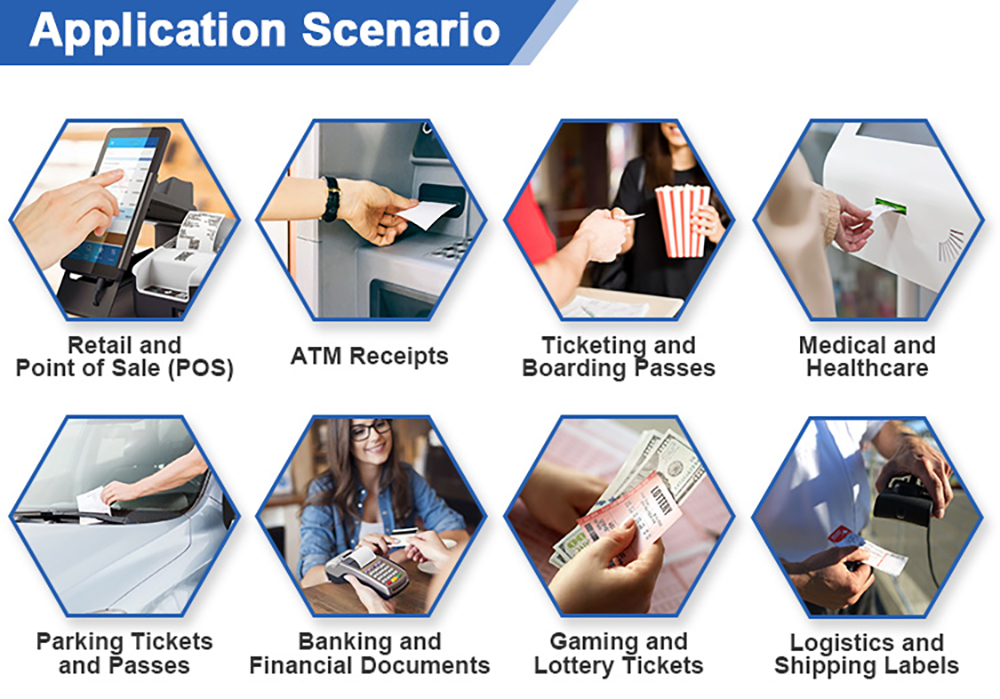
For multi-computer roll paper commercial paper products, the first single-link printing is required, and holes, ridge lines, and zigzag-shaped folds are taken and then the pages are sorted. In production, coding is the last step and it is done on the collating machine. In order to prevent the printed multi-finished bills from being misaligned in the collation, it is necessary to press the multiple bills together by the embossing teeth on the collator. Because it is web printing, the expansion and contraction rates of papers on different layers are not necessarily the same. Therefore, changes in the length of each single link after printing will cause many problems and even make the matching impossible.
Factors affecting paper length changes
1. Tension
Tension is the stretching force of the paper feeding system on the paper during the printing process. Excessive tension in the printing process will stretch the paper. After the printing, the tension is relieved. The paper will inevitably retract, causing the length of the paper to be shorter and shorter. Match page.
2. Paper moisture content
Different paper moisture content can also cause changes in the length of the paper. The greater the moisture content of the paper, the more severe the shrinkage of the printed paper.
3. Paper quantification
Under the same tension, the greater the amount of paper used for printing (thicker paper), the more severe the shrinkage of paper after printing, but also take into account the fact that thick paper has a large amount of water, under normal circumstances, thick paper should increase the tension.
Precautions
(1) During the printing process, a type of paper with the same brand and the same thickness should be used as much as possible so that the tension can be kept constant during printing.
(2) In actual production, even if the same brand, the same thickness of paper, the water content of the paper is also different, we must pay attention to its identification. The method of touching by hand can generally make the paper with a large moisture content cool and astringent, and the paper with the same width and length, with a large amount of moisture, can be heavier. Therefore, the tension should be appropriately reduced. However, we must pay attention to the suitability of paper. We can put paper in the production workshop for a certain period of time to adapt to the temperature and humidity of the workshop, so as to solve the problem of paper moisture content.
(3) When encountering multiple orders of different quantitative or different types of paper, attention should be paid to the adjustment of tension. First, in the printing of a joint, measuring with a hole length of 3m or more, and releasing 2~4mm than the standard length, to make up for the paper shrinkage caused by water loss: Secondly, when printing the second joint, it is also necessary to use The 3m hole distance gauge measures the paper hole pitch. If the paper is thick, it can be released 1~2mm more than the standard length. The paper has high water content and a large shrinkage factor. This will be based on the thickness of each paper in the United Nations to give different amount of increase in the spacing, so that each sheet of paper can be maintained at the same time.
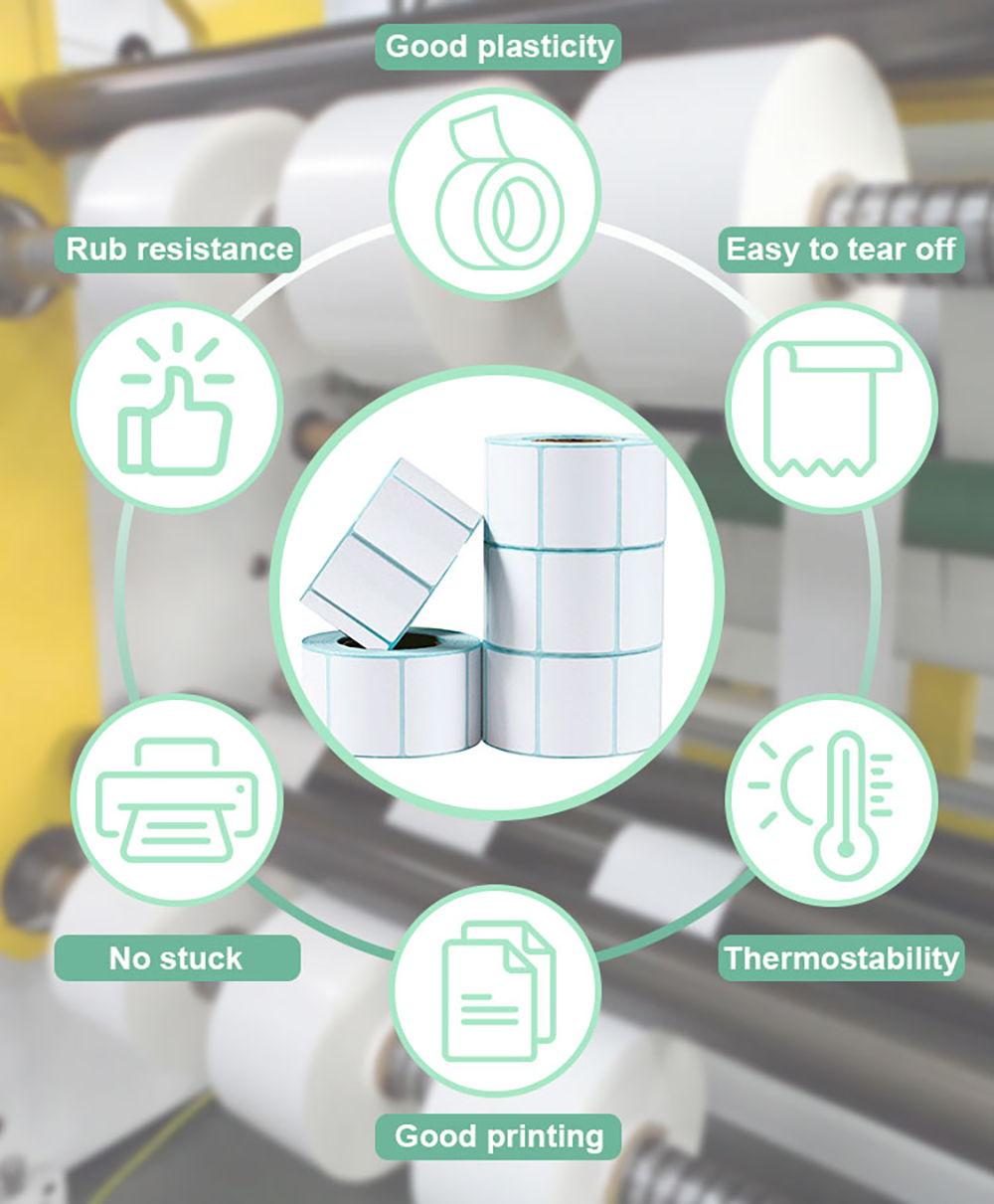
In spite of the above problems, complex sizing problems are occasionally encountered in multi-single printing, such as thermal paper with a basis weight of 180 g/m2 + offset paper with a basis weight of 70 g/m2 + basis weight of 40 g/m. The m2's carbon-coated dictionaries on the reverse side of the paper + color-paper coated paper + thinner paper sometimes meet with 10 pages of different pages. In this case, do not rush to work hands-on, layer by layer with the hole length combined with paper thickness. Moisture content was measured and even 3m each paper could be taken before printing. The paper was ventilated and dried, and the shrinkage coefficient was counted. After comparison, it was decided to apply different tensions. After each printing, it must be tightly wrapped with plastic film to prevent loss of waterproofing and cause difficulties in the matching.
Remedy
If there is a problem with the collation, you can take the following measures to remedy:
(1) The paper is longer and can be ventilated and dried to shorten it.
(2) When collating, a humidifier can be installed under a short joint to increase paper moisture and extend the paper.
(3) If the paper is shortened, you can increase the resistance of the paper during the passage of the paper while using the humidifier. For example, add sponge on the paper rod to increase the resistance and make the paper stretch.
If you use the above method to arrange pages, do not ventilate them. Pack them in plastic boxes and store them in pressure.
Commercial paper printing has very strict requirements on the environment temperature and humidity, especially the requirements on the environment humidity, so we must try to control it without drastic changes. At the same time after printing should be immediately wrapped with plastic film, but can not be placed for too long, should be allocated as soon as possible to prevent the environment temperature and humidity changes caused by paper stretching and affect product quality.
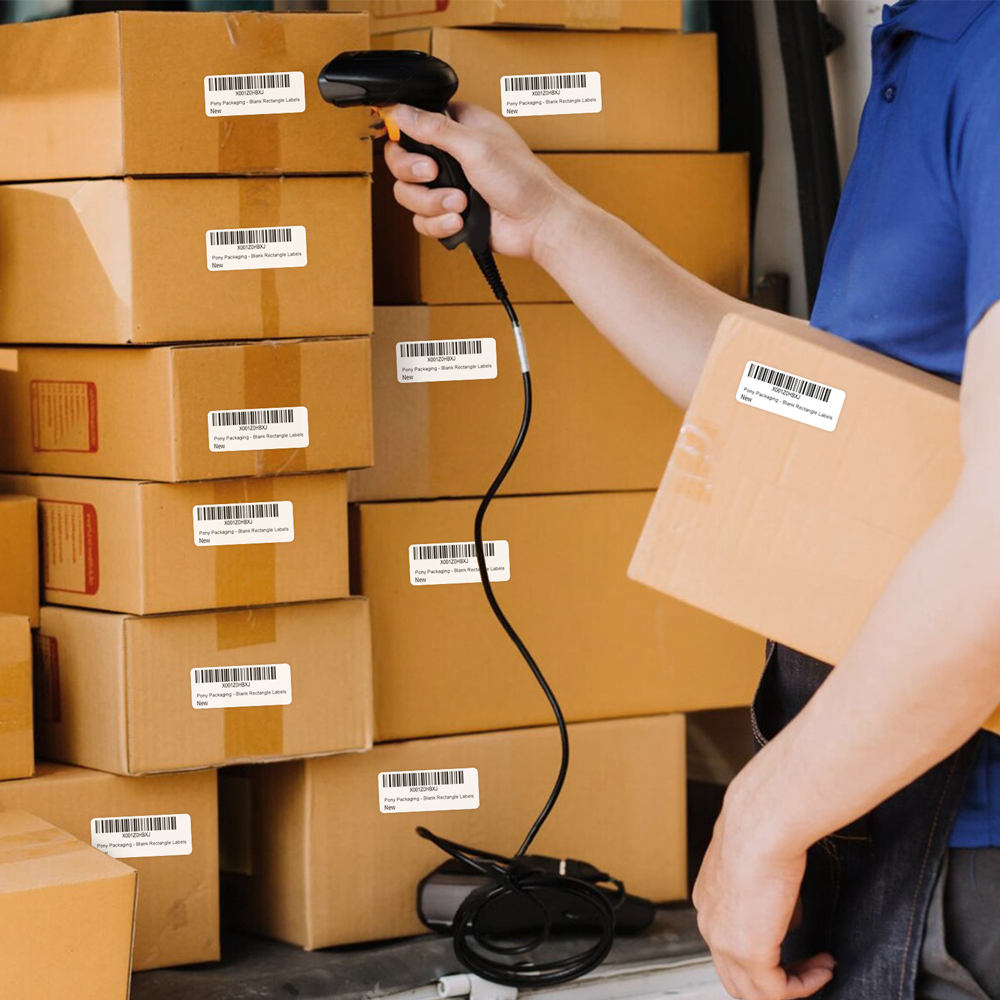